TM 55-2210-223-34
TO 45A2-2-14-22
4-8.
AIR COMPRESSOR (cont)
CLEANING, INSPECTION, AND REPAIR (cont)
(3)
Use feeler gage between connecting rod cap (93) and journal of crankshaft (115) and check for a
measurement of 0.0015 inch (0.038 mm) maximum clearance.
(4)
Turn connecting rod (90) 1 inch (25.4 mm) at piston pin end and check that connecting rod turns freely.
(5)
Check for maximum clearance in same manner as in step (3) above. Clearance between connecting rod
cap (93) and crankshaft journal (115) must be 0.003 inch (0.076 mm) maximum.
(6)
Turn connecting rod (98) 1 inch (25.4 mm) at piston pin end and check that connecting rod turns tightly.
e.
Use a feeler gage and measure side clearance of connecting rod (98). Side clearance limits are 0.002 inch (0.05
mm) minimum and 0.031 inch (0.79 mm) condemnable.
f.
Remove connecting rods (98), bearings (93), and caps (89) from crankshaft (115).
g.
Replace damaged connecting rods (98).
49.
Clean, inspect, and repair oil pump plunger (104) by the following:
a,
Use drycleaning solvent and remove dirt and oil from oil strainer screen (110). Dry with compressed air.
b.
Check that oil strainer screen (110) is not frayed or damaged. Replace damaged screen.
c.
Use a feeler gauge and measure radial clearance between oil pump plunger collar and crankshaft eccentric
journal. Clearance limits are 0.003 inch (0.08 mm) minimum and 0.005 inch (0.13 mm) condemnable. If
clearance limits are exceeded, replace oil pump plunger (104).
d.
Check that ball and ball seat of oil plunger (104) are not worn or damaged by the following:
(1)
Use a micrometer and measure from end of oil pump plunger (104) to bottom of ball. Wear limits are
0.271 to 0.225 inch (6.88 to 5.72 mm). If wear limits are exceeded, replace plunger.
(2)
If ball inside oil pump housing (105) is damaged, replace with new stainless steel ball.
4-18
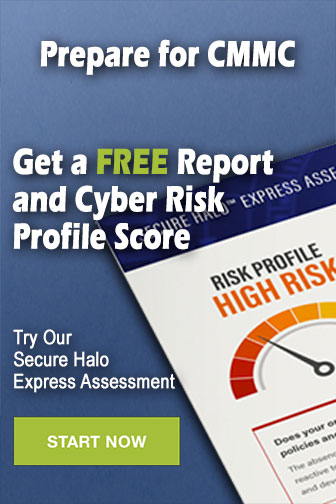