TM 55-2210-223-34
TO 45A2-2-14-22
4-8.
AIR COMPRESSOR (cont)
ASSEMBLY (cont)
68.
Install oil strainer screen (110) into oil strainer body (108) and secure with retainer ring (109).
69.
Install oil pump housing (105) into crankcase (116).
70.
Install assembled oil strainer body (108) and secure with capscrew (106).
71.
Install oil pump plunger (104) in oil pump housing (105) and around crankshaft (115).
72.
Install cap (103) on crankshaft (115) and secure with four bolts (101), nuts (102), and cotter pins (100). Refer to
table D-1 for torque values.
73.
Install key (111).
74.
Install two upper bearings (92) on connecting rods (98).
75.
Install pistons (90), and (91) on connecting rods (98).
76.
Install two piston pins (97) into connecting rods (98) and pistons (90) and (91) and secure with four snap rings (96).
77.
Install four piston rings (94) on piston (90) and four piston rings (95) on piston (91).
NOTE
Check that punch marks are alined when installing heads and cylinders.
78.
Install gasket (86), high-pressure cylinder (85), and six nuts (84). Tighten nuts evenly and pull high-pressure
cylinder in place.
79.
Install gasket (83), low-pressure cylinder (82), and six nuts (81). Tighten nuts evenly and pull low-pressure cylinder
in place.
80.
Use oil and lubricate crankshaft journal throw, cylinder walls, connecting rod bearings, piston rings, and piston pins.
81.
Stagger piston ring gap and install piston (91) in high-pressure cylinder (85).
82.
Stagger piston ring gap and install piston (90) in low-pressure cylinder (82).
83.
Install two upper bearings (92) and lower bearings (93).
84.
Install four bolts (99), two connecting rod caps (89), and four castle nuts (88). Tighten nuts to 125 ± 50 lb-ft (170 ±
68 N.m) and aline castle nut with holes in bolts, and secure with four cotter pins (87). Refer to table 4-1 and check
ring gap and cylinder-to-piston clearance.
4-23
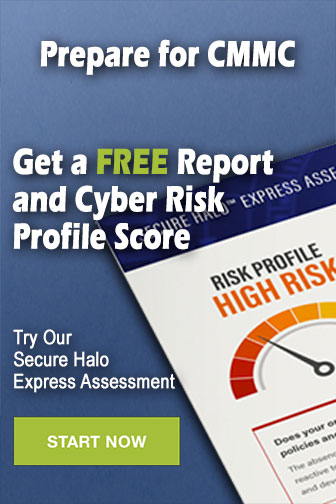