TM 55-2210-223-34
TO 45A2-2-14-22
4-8.
AIR COMPRESSOR (cont)
ASSEMBLY (cont)
103. Install dipstick (55), oil pressure gauge (54), and crankcase breather (53).
104. Install gasket flange (52), intake tube (51), rubber gasket (50), and intake strainer (49) and secure with two bolts
(48).
105. Install gasket flange (14), discharge flange (13), and four locknuts (12).
106. Install air baffle (11), cooling fan (8), nut (7), and cotter pin (6) and secure with eight lockwashers (10) and bolts (9).
107. Install extension (5) and discharge elbow (4).
108. Install fan guard (3) and secure with 12 lockwashers (2) and capscrews (1).
109. Refer to paragraph 3-44 and install and aline air compressor.
110. Fill crankcase with oil and install filler plug (43).
TEST
CAUTION
When performing orifice test, check that oil pressure is never less than 15 psi (103 kPa). Damage to air
compressor can result.
111. Perform an orifice test by the following:
a.
Connect an orifice holder with 17/64-inch (6.7 mm) orifice in air reservoir drain cock. Use orifice with square
edges bored through plate 1/16 inch (1.6 mm) thick.
b.
Start engine and run until it is at normal operating temperature.
c.
Close outlet valve from reservoirs and open drain cock. Leave drain cock open for all tests.
d.
Run air compressor at least 2 minutes at low speed (table 4-2) and take a pressure reading. Record air
compressor speed (rpm) and corresponding pressure.
e.
Run air compressor at least 2 minutes at high speed (table 4-2) and take a pressure reading. Record air
compressor speed (rpm) and corresponding pressure.
f.
Run air compressor 15 minutes (drain cock open) and repeat steps d and e.
g.
Use table 4-3 and compare speed-pressure readings.
4-25
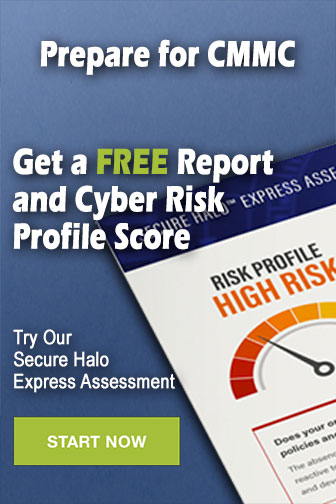