TM 55-2210-224-34
4-8.
AIR COMPRESSOR ASSEMBLY (cont)
CLEANING, INSPECTION, AND REPAIR (cont)
g.
Install crankshaft (166) between centers in a lathe and check runout. Maximum runout is 0.001 inch (0.0254
mm).
h.
Replace damaged crankshaft (166).
38. Clean, inspect, and repair low-pressure cylinder (100) and high-pressure cylinder (106) by the following:
a.
Use drycleaning solvent and remove dirt, grease, and oil from low-pressure cylinder (100) and high-pressure
cylinder (106). Dry with compressed air.
b.
Check that ring travel surface is not scored and does not have ridges.
c.
Use a honing drill and hone cylinder walls to a bright, smooth finish (25 to 40 micro-inches and a cross hatch
pattern of 25 to 35 degrees).
d.
Inspect perpendicularly of low-pressure cylinder (100) and high-pressure cylinder (106) with flange face by
the following:
(1) Install low-pressure cylinder (100) and high-pressure cylinder (106) in a lathe or boring mill.
NOTE
If cylinder flanges are machined, check that cylinder length is not shortened beyond
the minimum limit. This is determined by installing piston in upper dead center
position and ensuring piston is flush or below top face of cylinder.
(2) Use an inside micrometer and measure both ends of cylinder bore for taper. Maximum variance is 0.002
inch (0.0508 mm). If variance exceeds maximum, machine cylinder flanges.
e.
Use a feeler gage and measure cylinder-to-piston clearance. Refer to table 4-1 for clearance dimensions. If
cylinder-to-piston clearance is not within limits, replace piston with a new, standard size piston. Recheck
cylindertop piston clearance. If not within limits, replace low-pressure cylinder (100) and high-pressure
cylinder (106) with a new, standard size cylinder.
f.
Replace damaged low-pressure cylinder (100) or high-pressure cylinder (106).
39. Clean, inspect, and repair pistons (133) and (140) by the following:
a.
Use drycleaning solvent and remove dirt, grease, and oil. Dry with compressed air.
b.
Magnaflux pistons (133) and (140) and check that there are no cracks.
c.
Check that piston ring grooves are square and do not have ridges.
4-20
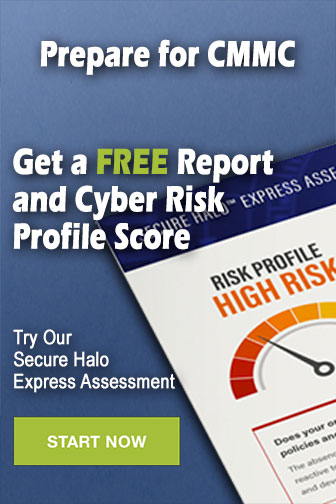