TM 55-2210-224-34
4-8.
AIR COMPRESSOR ASSEMBLY (cont)
CLEANING, INSPECTION, AND REPAIR (cont)
d.
Use a feeler gage and measure clearance between ring sides and grooves. Clearance is 0.002 to 0.004
inch (0.0508 to 0.1016 mm).
e.
Use a micrometer and measure piston skirts. Refer to table 4-1 for diameter limits.
CAUTION
Do not use a stone or emery cloth to remove minor scuff marks or scratches from
pistons (133) and (140). Damage to pistons will result.
f.
Use a file and remove minor scuff marks and scratches from pistons (133) and (140).
g.
Replace damaged pistons (133) and (140).
40.
Clean, inspect, and repair connecting rods (130) and (137) by the following:
a.
Use drycleaning solvent and remove dirt, grease, and oil from connecting rods (130) and (137). Check
that oil passages are free of obstruction. Dry with compressed air.
b.
Magnaflux connecting rods (130) and (137) and check that there are no cracks.
c.
Inspect connecting rod bolts (117) and (123) and nuts (116) and (122) and check that threads are not
damaged. Check that nuts turn freely on bolts.
d.
Check that connecting rods (130) and (137) are fitted to crankpin of crankshaft (166) by the following:
(1)
Apply a film of light oil on crankpin.
(2)
Install connecting rods (130) and (137) and torque nuts (116) and (122) to 75 to 80 lb-ft. Check
that nuts are lined up to meet cotter pin holes in bolts.
(3)
Install a 0.001-inch (0.0254 mm) feeler gage between bearing caps (118) and (124) and
crankpin. Check that feeler gage extends entire width of rod cap bearing surface.
(4)
Turn connecting rods (130) and (137) 1 inch (25.4 mm) at piston pin end and check that
connecting rod turns freely.
(5)
Remove 0.001-inch (0.0254 mm) feeler gage and install 0.003-inch (0.0762 mm) feeler gage.
Repeat step (3) above.
(6)
Turn connecting rods (129) and (136) 1 inch (25.4 mm) at piston pin end and check that
connecting rod turns tightly.
4-21
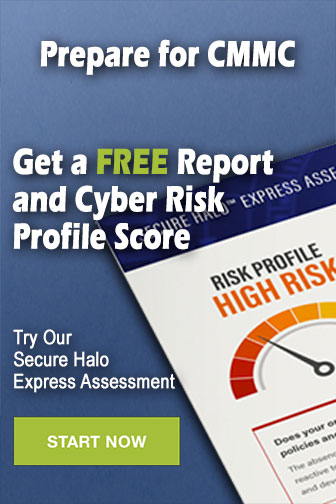